I Saw the Future in Columbia’s Nanotechnology Clean Room
Credit to Author: Caroline Haskins| Date: Tue, 19 Sep 2017 12:00:00 +0000
If you ever want to feel like a mad scientist, I highly recommend spending a day in a clean room.
I got the chance to spend an afternoon at Columbia University’s Clean Room, a newly renovated $20 million facility for nanoscience projects so sensitive that one spare particle can ruin them. Researchers are transmitting data using light, developing lidar (light-radar) for driverless cars, and creating 2D “superatoms” that can represent quantum behavior.
But entering the cutting edge of nanotechnology means taking an elevator to the tenth floor, covering almost your entire body in layers of nylon and nitrile, and entering a murky, windowless space of orange light.
—
“Thin film” research is a hallmark of the Clean Room—a process by which electronics are built from molecule up. John Kymissis, a professor of Electrical Engineering and Applied Sciences at Columbia, said that this enables precise specialization of electronic equipment.
“I like to think of thin film electronics as a toolbox in which we reach in and grab the materials that we need,” he said.
According to Michal Lipson, a professor of Applied Physics at Columbia, thin film research has also enabled leaps in neuroscience. Silicon needles just a few microns thick can be prodded into the brains of mice in order to target individual neurons.
“Basically, we can make the animal do whatever is expected in terms of behavior,” she said. “That’s the Holy Grail—understanding and controlling the brain functionalities, and it requires extreme control of exciting the neurons.”
The Clean Room serves over 300 users from Columbia, CUNY, and private firms.
James Vichiconti, the Director of the Clean Room, led me on a tour of the Clean Room. Between the hallway and the Clean Room, there’s an area that acts as a mud room. Dim, orange light was used in the room to protect projects in the adjacent room, which are sensitive to ultraviolet light.
After a sticky welcome mat removed the dirt particles from my shoes, I was greeted by a 10-foot long rack of nylon “clean suits,” and boxes upon boxes of shoe covers, hair nets, eye goggles, hair nets, and even beard covers, which Vichiconti calls “the hipster covers.”
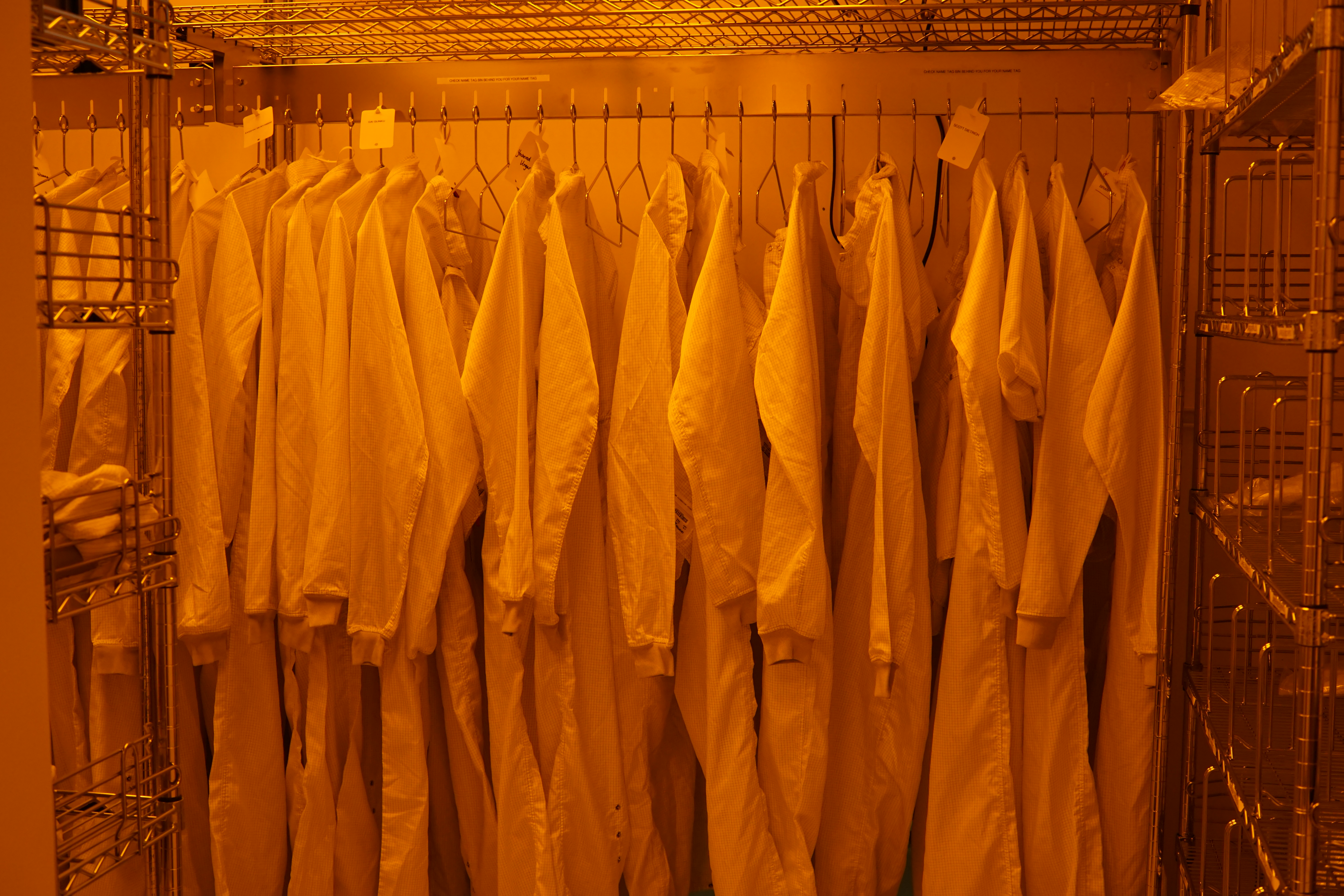
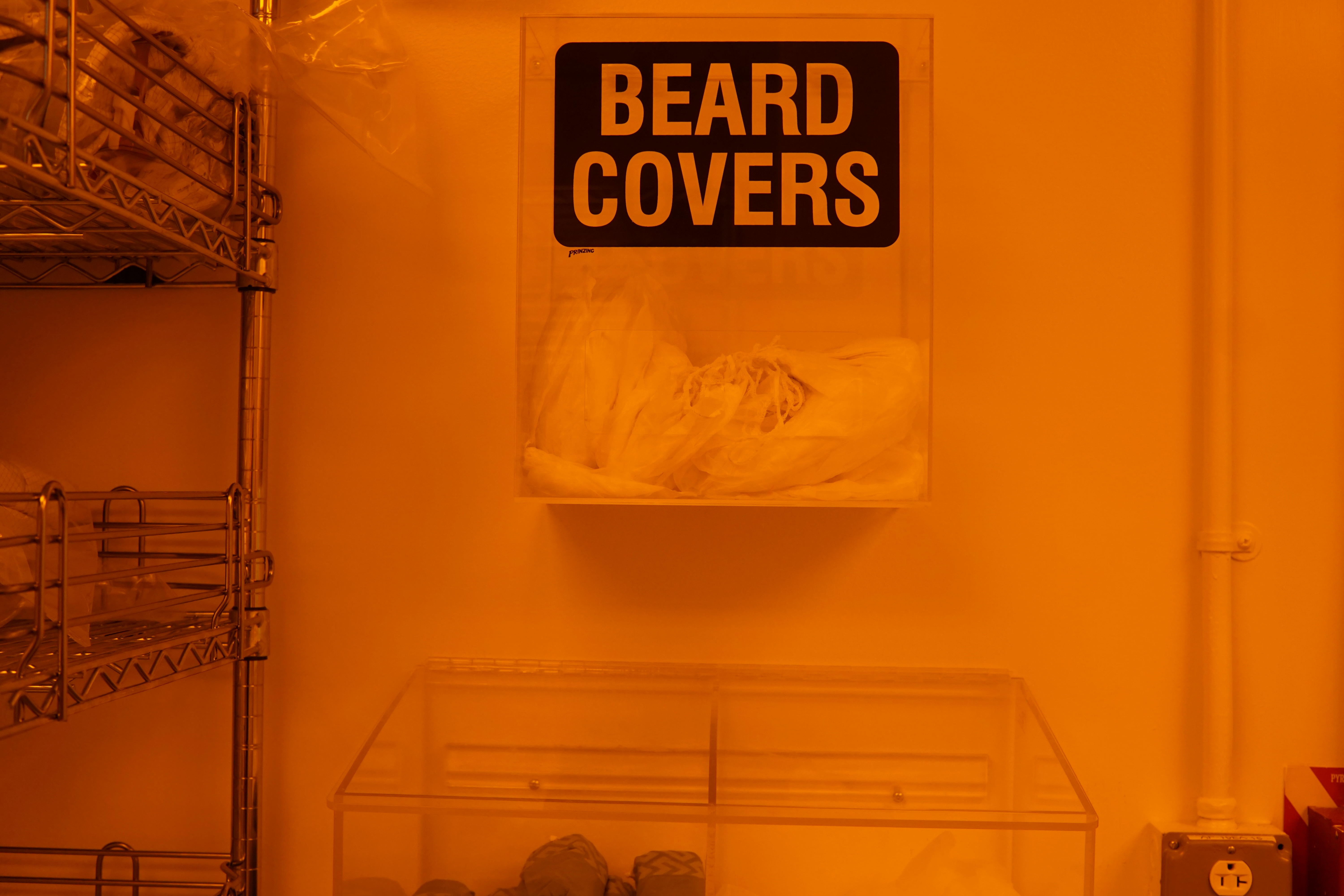
Through a glass window, I saw a student placing a small item into a machine about the size of a turn-of-the-millennium iMac. Vichiconti told me to wait before taking a picture, because the student’s project was sensitive to the flash from my camera.
When the student entered the mud room she told me her name is Christine McGinn, a second-year Columbia graduate student. She told me she was printing a 2D thin film electroconductive mask. When these films are layered, she can create a 3D piece of electronics which can be tailored for robotics, medical equipment, microphones, toxic vapor sensors, or cellphone circuits.
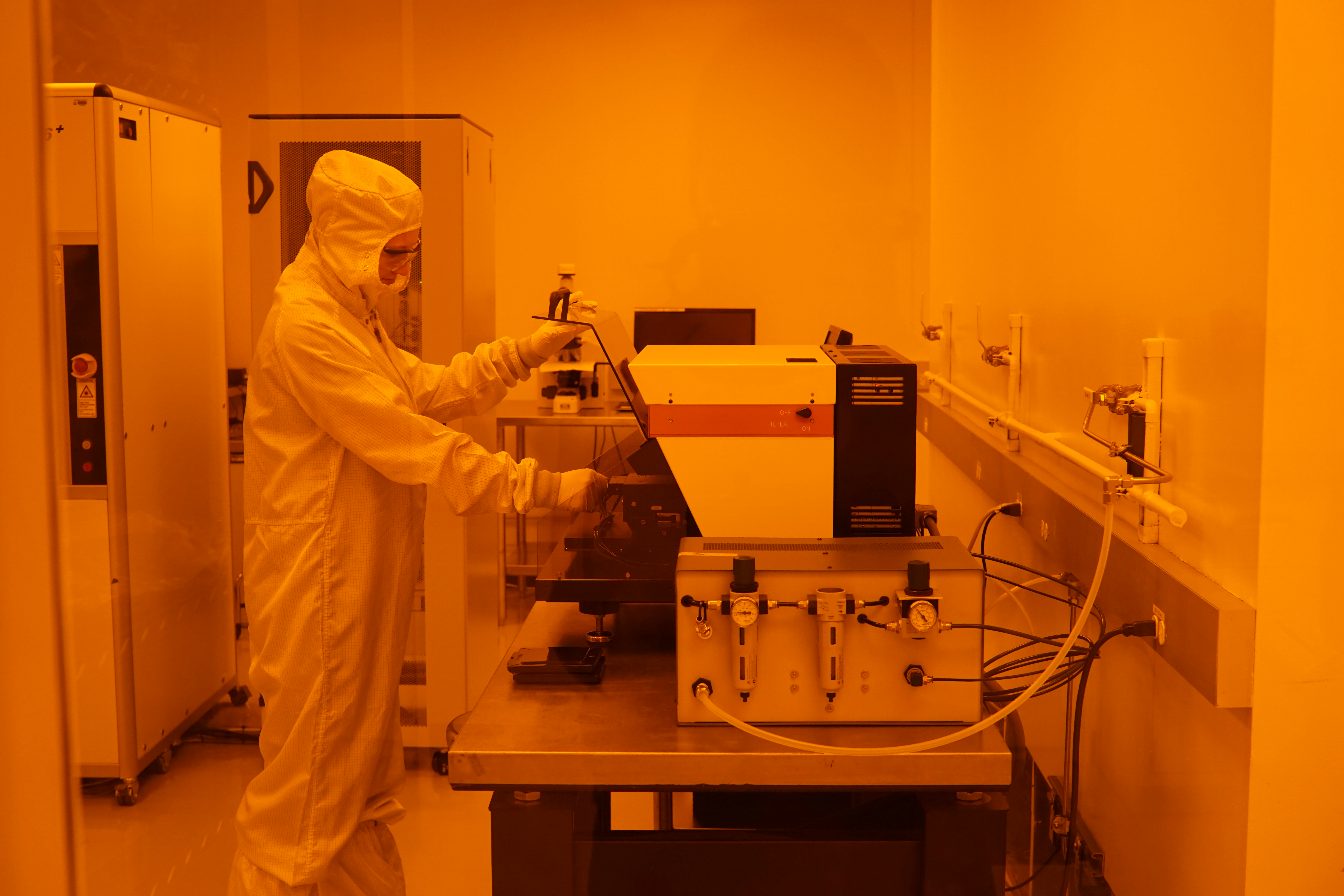
“[Thin film] is in literally everything right now—you carry it around in your pocket every day, and it’s nice to know how the tiny structures in your phone, your camera, and all those other things appear,” McGinn said. “Also, it makes you feel like a mad scientist to wear the suit.”
After not-so-subtly suggesting that I wanted to see the Clean Room firsthand, Vichiconti was kind enough to lend me some dungarees to wear over my skirt. Research Operations Assistant Melody Gonzalez then showed me how to put on a clean suit, which took about five minutes.
First, I had to put my bangs and braid inside a hair net, and under a nylon head mask. Then I slipped into a nylon clean suit and shoe covers which rose up to my knees. I also wore plastic eye goggles and sterile gloves. (Gonzalez recommended the nitrile gloves, which were softer than the latex gloves.)
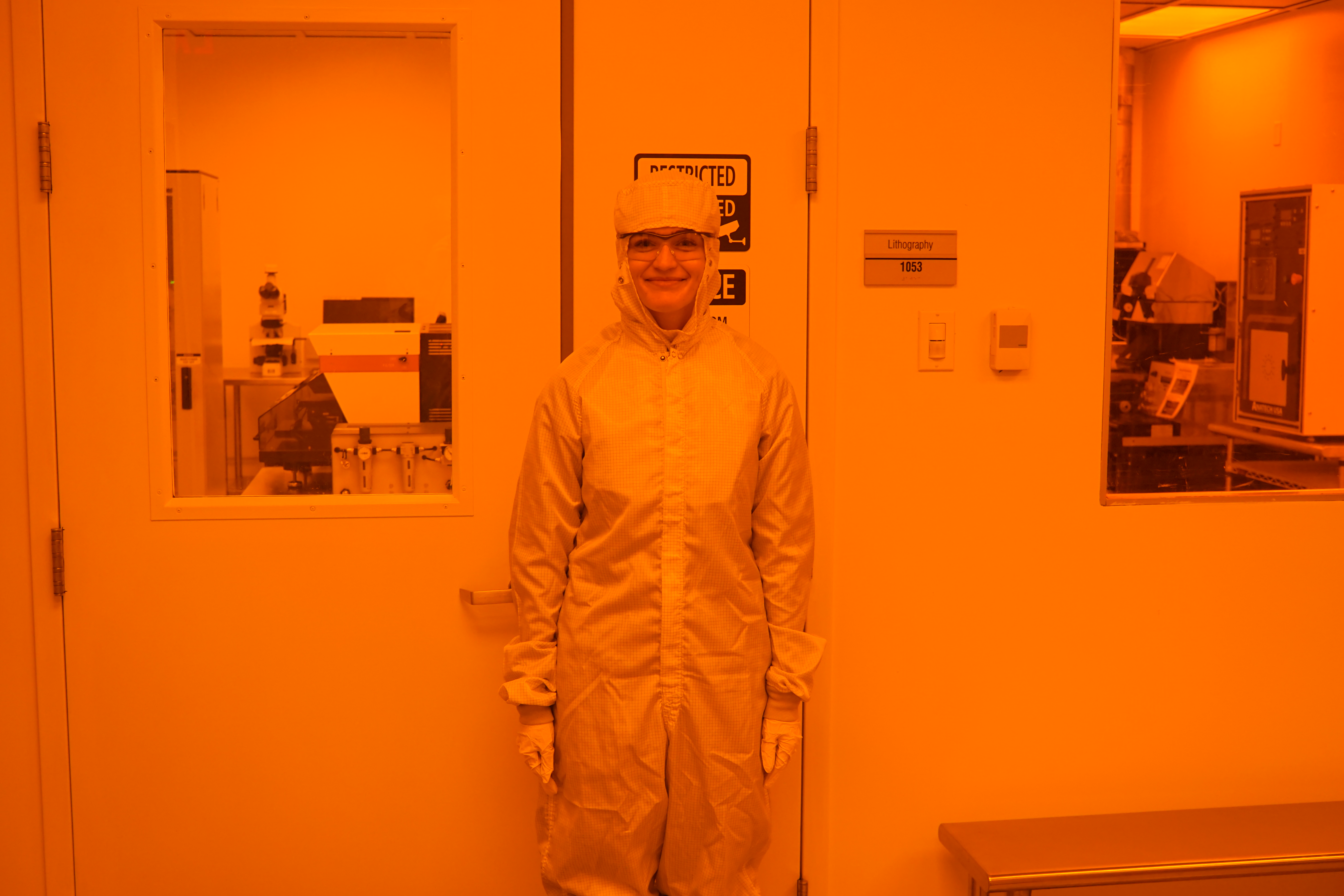
The suit makes you look more like a plastic thumb than a disaster movie hero, but I was grateful to get a close-up look at the Clean Room’s state-of-the-art equipment.
After crossing the threshold into the Clean Room, Gonzalez first brought me toward a refrigerator attached to a circulation vent and three massive silver machines.
She said that the refrigerator used to smell “like death” because of photoresist—a pungent substance crucial in thin film electronics. But the new ventilation system neutralized the smell.
Multiple people throughout the day emphasized the intricate ventilation and piping. During the morning symposium, Columbia Nano task force co-chair James Hone said that the modern piping was the biggest difference from the old Clean Room, since not all of the equipment is brand now—some machines are a few months to a few years old.
“The real work is up in the ceiling, behind the walls,” he said. “It’s the Mona Lisa of piping. It’s like the train lines running underneath Penn Station.”
The silver machines next to the refrigerator are Reynoldstech fabricators, which prepare thin film samples. Gonzalez said that the flash from my camera could trigger a series of reactions that release toxic gases inside the fabricators, so I decided not to take a picture.
As it turns out, the Clean Room is not just one room. Gonzalez led me into an adjacent, brightly-lit room designed for research that is less sensitive to ultraviolet light. She said that the Angstrom is the most popular tool in the room. It has electron beam, heat, and pressure systems that are used in a variety of thin film projects.
Gonzalez said that people cried during a three-month period in the Clean Room renovation that kept them from the Angstrom. I asked if she was serious.
“Not cried, but I saw it their eyes,” she said. “They were really sad that they weren’t able to use it.”
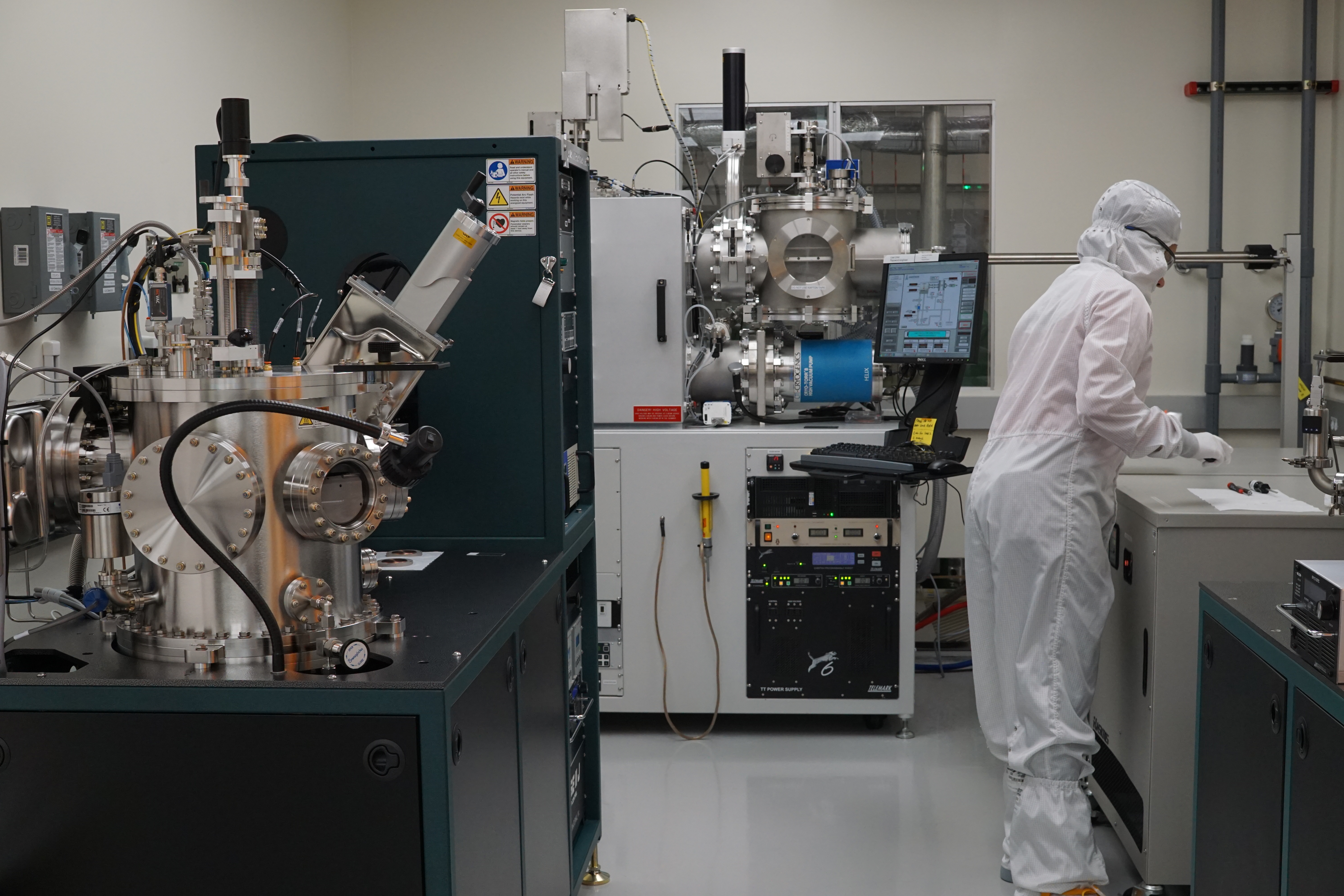
Even now, access to the Angstrom and the rest of the Clean Room is limited. Before the Fire Department approves Columbia’s safety regulations, Clean Room access is limited to 11 hours per day during the week rather than 24/7.
“As soon as the thing is open 24 hours, from wherever you are, you will hear the users scream in joy,” Gonzalez said.
Gonzalez also showed me what Vichiconti described as the “macro room.” There, the thin film samples prepared in the other two rooms are painstakingly assembled in order to create a functioning piece of nano-scale electronics.
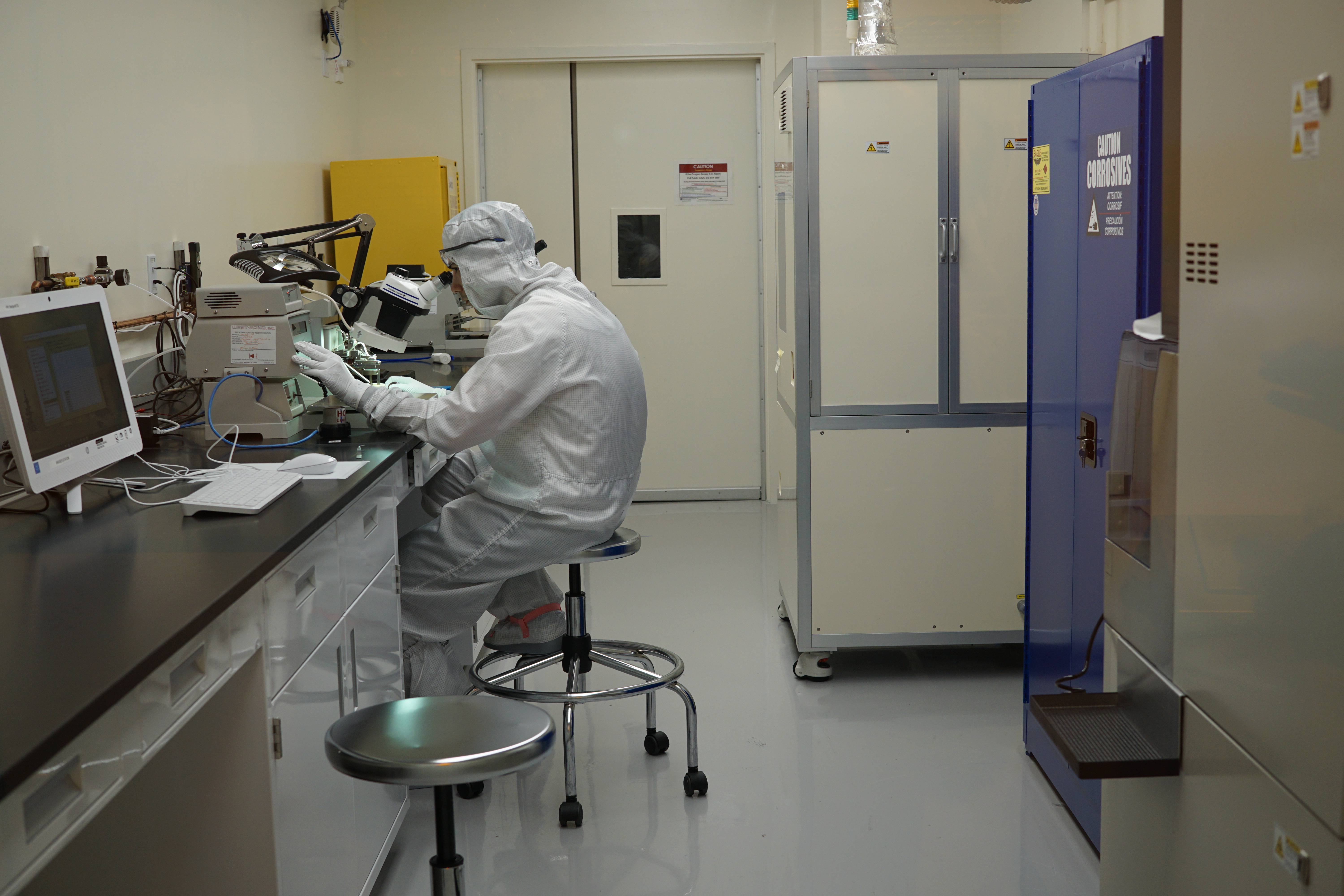
Before leaving, I asked Gonzalez what drew her to the Clean Room’s Research Operations.
“Restocking gloves, restocking shoe covers, making sure chemical waste is picked up—it’s not the most exciting thing,” she said. “But when you have a team that treats you like family, and you have users that respect you and thank you for what you do, you feel like you’re actually contributing something. It’s really cool to know that you’re a part of something bigger than yourself.”